Stronger Soft Robotics Improves VR Gloves, Opening New Applications
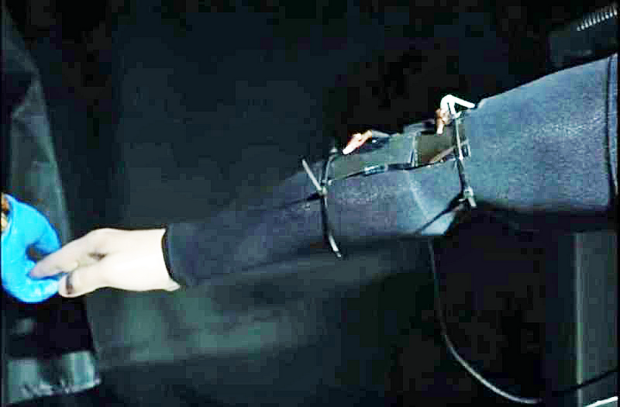
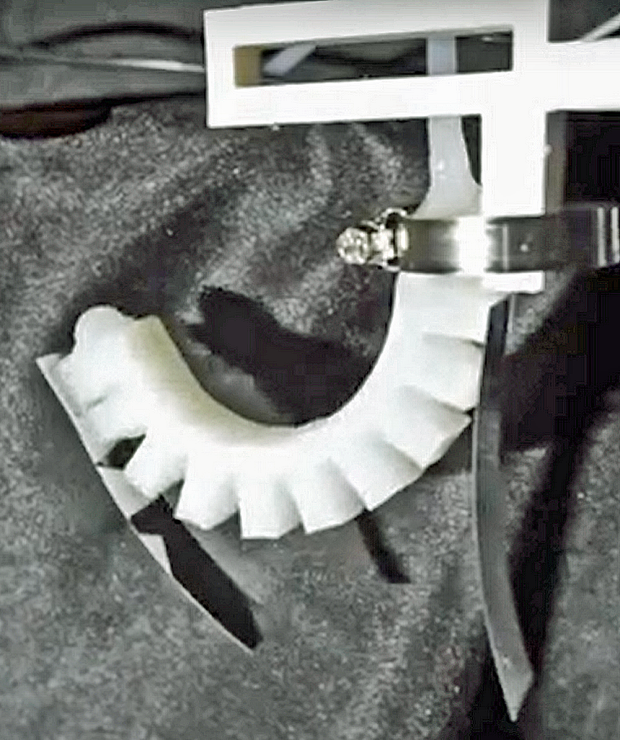
Soft robots, or those made with materials like rubber, gels and cloth, have advantages over their harder, heavier counterparts, especially when it comes to tasks that require direct human interaction. Robots that could safely and gently help people with limited mobility grocery shop, prepare meals, get dressed, or even walk would undoubtedly be life-changing. However, soft robots currently lack the strength needed to perform these sorts of tasks. Making soft robots stronger without compromising their ability to gently interact with their environment has limited the development of these devices. Penn Engineers at the University of Pennsylvania School of Engineering and Applied Science have devised a new electrostatically controlled clutch that enables a soft robotic hand to be able to hold 4 pounds, 40X more than the hand could otherwise lift. This required 125 volts, a third of the requirement for current clutches.
James Pikul, Assistant Professor in Mechanical Engineering, Kevin Turner, Professor and Chair of MEAM, and their Ph.D. students, David Levine, Gokulanand Iyer and Daelan Roosa, published a study in Science Robotics describing a new, fracture-mechanics-based model of electroadhesive clutches, a mechanical structure that can control the stiffness of soft robotic materials. Using this new model, the team was able to develop a clutch 63X stronger than current electroadhesive clutches. The model not only increased force capacity of a clutch used in soft robots, it also decreased the voltage required, making soft robots both stronger and safer.
An electroadhesive clutch is a thin device that enhances the change of stiffness in the materials which allows the robot to perform this task. The clutch, similar to a clutch in a car, is the mechanical connection between moving objects in the system. In the case of electroadhesive clutches, two electrodes coated with a dielectric material become attracted to each other when voltage is applied. The attraction between the electrodes creates a friction force at the interface that keeps the two plates from slipping past each other. The electrodes are attached to the flexible material of the robotic hand. By turning the clutch on with an electrical voltage, the electrodes stick to each other, and the robotic hand holds more weight than it could previously. Turning the clutch off allows the plates to slide past each other and the hand to relax, so the object can be released.
Traditional models of clutches are based on a simple assumption of Coulombic friction between two parallel plates, where friction keeps the two plates of the clutch from sliding past each other. However, this model does not capture how mechanical stress is non-uniformly distributed in the system, and therefore, does not predict clutch force capacity well. It is also not robust enough to be used to develop stronger clutches without using high voltages, expensive materials, or intensive manufacturing processes. A robotic hand with a clutch created using the friction model may be able to pick up an entire bag of apples, but will require high voltages which make it unsafe for human interaction.
"Our approach tackles the force capacity of clutches at the model level," says Pikul. "And our model, the fracture-mechanics-based model, is unique. Instead of creating parallel plate clutches, we based our design on lap joints and examined where fractures might occur in these joints. The friction model assumes that the stress on the system is uniform, which is not realistic. In reality, stress is concentrated at various points, and our model helps us understand where those points are. The resulting clutch is both stronger and safer as it requires only a third of the voltage compared to traditional clutches."
"We haven't seen many soft robots in our world yet, and that is, in part, due to their lack of strength, but now we have one solution to that challenge," says Levine. "This new way to design clutches might lead to applications of soft robots that we cannot imagine right now. I want to create robots that help people, make people feel good, and enhance the human experience, and this work is getting us closer to that goal. I'm really excited to see where we go next." To learn more, visit the Phys.Org Techxplore website here.